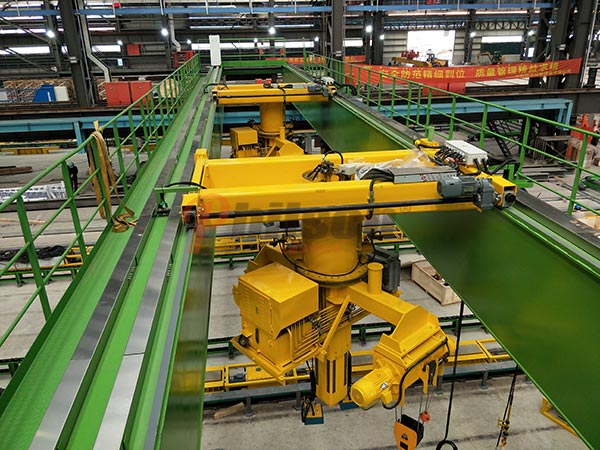
1、物品的识别、校验、反馈与信息存储技术
根据被吊物品的形态、包装方式、储运方法等,常 见被吊物品包括:卷(钢卷、纸卷、薄膜卷等)、箱(集 装箱、料箱、转运箱等)、块(钢板、钢胚、盾构构件等)、捆(钢管、螺纹钢、轨道、型钢等)、盘(电缆、 盘条等)、件(斗、包等)、根(轨道、工字钢、H 形钢、梁等)。
各种状态物品的自动识别、检验和反馈是数据的编码、采集、标识、管理、传输的标准化手段,是智能起重机的工作基础。该技术涉及物品信息数据的编码、采集、标识、管理、传输等过程。包括条 码识别、RFID 射频识别、语音识别、光 字符识别、磁识别等特 定格式信息识别技术和图像、图形识别、生物特征识别等图像、图形格式信息识别技术。识别、检验后存储的物品信息需具备普遍性、唯一性、稳定性和不可复制性。
2、空间定位技术
国内部分高端产品虽然应用了三维定位技术,但定位水平受限于整机系统的累积误差,不能实现高精度定位。目前普遍应用的定位方式有2类:一类是相对认址,一般采用旋转编码器、激光或雷达测距、视觉识别等方式实现;另一类是绝对认址,一般采用位置限位开关、编码电缆(格雷母线)、线性编码器、 BPS 条码、链轮链条以及实时绝对认址无线电、红外线、无线射频、GPS 等方式实现。伴随无线通讯技术的进步,通讯网络的蜂窝定位及WiFi、蓝牙、红外线、超宽带、RFID和超声波等室内无线定位技术的定位精度越来越高,已逐步在机械设备的定位推广应用。
起重机定位技术不仅涉及被吊物品的外形监测、空位探测、实际存放位置的一维、二维、三维认址和定位方法,还涉及起重机取物装置(吊钩、货叉、吸盘、抓具、抓斗等)的一维、二维、三维认址和定位方法。
由于起重机的作业范围较大,单一的定位方法难以达到需要的定位精度,故大区域、复杂环境下的精确定位常采用“相对趋近寻址+绝对定位认址”的综合定位技术,相比单纯的绝对认址或相对认址定位的方式,具有更准确、更稳定、更经济,对土建工程质量的要求更低,更能适用起重设备恶劣的环境。
3、智能取物装置
95%以上的起重机取物装置都采用吊钩,只能采取人工摘挂,吊运某一类特定物品,通用性差,制约了起重搬运设备自动化程度的提高。在吊取和搬运散料、箱、捆、卷等不同物品过程中,智能起重机需配套自动取物装置或智能吊具,包括自动摘挂吊钩、C 形钩、电磁吸盘、真空吸盘、货叉、夹钳、夹具、挂梁、箱式吊具、罐、抓斗、抓具等。根据各类被吊物品的状态,研发适合起重机应用的自动取物装置或智能吊具,实现起重机的自动存取,是起重机实现智能化的最关键环节。
4、路径规划与柔性升降系统的电子防摇摆技术
运行路径规划和柔性升降系统的防摇摆定位控制是实现起重机运行的必要条件。起重机在工作过程中,大、小车加减速以及负载的提升都会使负载出现来回摆动,不仅影响起重机作业效率,还会引发事故。目前常用开环和闭环控制技术实现起重机路径规划和防摇摆控制。开环控制方法主要包括基于输入整形的定位防摇摆控制和基于轨迹规划的定位防摇摆控制。实现路径规划和防摇摆的闭环控制方法有很多,如反馈线性化、增益调度控制、滑模控制、预测控制、模糊控制、神经网络控制、无源性控制等控制方式。
对于障碍物地点固定不变的吊装和搬运环境,采用静态路径规划即可满足要求。但是,当环境中的障碍物不能事先确定或多台起重机混合作业时,需要采用动态路径规划的方法在线实时得到安全的路径。吊装的路径规划。近年来学者们针对起重机的路径规划给出了一些有效的规划算法,如人工势场法、概率路标算法、快速随机生成树算法、遗传算法、蚁群算法等。
随着无线移动通讯技术的发展,将感应器(陀螺仪、加速度传感器、方位传感器等)安装在吊具或取物装置上,实现基于被吊物品的三维定位、路径规划和防摇摆控制将得到广泛应用。
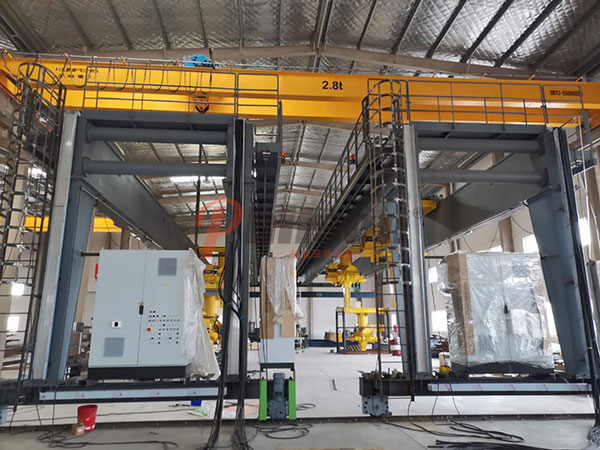
5、状态检测与故障自动诊断技术
状态监测是指通过一定的途径了解和掌握设备的运行状态;故障诊断则是根据状态监测所获得的信息,结合设备的工作原理、结构特点、运行参数、历史状况,对可能发生的故障进行分析、预报,对已经或正在发生的故障进行分析、判断,以确定故障的性质、类别、程度、部位及趋势。状态监测与故障诊断的意义在于其有效地遏制了故障损失和设备维修费用。
起重机械监控过程中的需要监控的常用监控参数包括起重量、起重力矩:起升高度下降深度;运行行程、幅度、大车运行偏斜;水平度;风速;回转角度;同一或不同一轨道运行机构安全距离;支腿垂直度;工作时间、累计工作时间、每次工作循环等。常用的监控状态 包括电机状态;制动器状态;变频器状态;抗风防滑状 态;联锁保护:门限位、机构之间的运行联锁;工况设置状态;供电电缆卷筒状态;过孔状态;以及视频系统、桥架刚度、强度实时自检测系统等。
6、实时在线监测及远程诊断技术
该系统包括传感器监测、实时无线传输、数据管理、信息查询、故障根源分析、趋势分析、专家诊断、状态 预知预测、物联网远程监控等技术。通过给现有设备安 装监控网关, 通过WiFi或3G网络传输数据采集运行状态和故障情况,实现远程监控和可视化管理;集成新设备自带的远程管理系统,建立统一的设备管理平台;与资产维修管理系统集成,提升维修效率和设备的工作表现。提供网络化的紧急维修协调配合机制,通过无线抄表获取设备实时状态,自动生成维修和检查计划,并在数据分析的基础上逐步实现基于状态的预知性维修 。
通过计算机网络实现的预知性维修以状态监测与故障诊断技术为基础,以设备实际状况为依据 ,根据生产需要制定预知性维修计划的维修体制。其目标是实现实时停车、对应换件、维修确定的项目。从目前的故障维修、定期计划维修,实现未来的预知 性维修,辨别故障的真伪,判断故障的类型、程度、具体部位,预判故障 发展的趋势。及时发现故障的早期征兆,以便采取相应的措施,避免、减缓、减少重大事故的发生;一旦发生故障,能自动纪录下故障过程的完整信息,以便事后进行故障原因分析,避免再次发生同类事故;通过对设备异常运行状态的分析,揭示故障的原因、程度、部位及趋势,为设备的在线调理、停机检修提供科学依据,延长运行周期,有效地遏制故障损失和设备维修费用;根据状态监测所获得的信息,结合设备的 工作原理、结构特点、运行参数、历史状况,对可能发生的故障进行分析、预报,可充分地了解设备性能,为改进设计、制造与维修水平提供有力证据。
7、成套装备的监控和管理
针对散料、箱、捆、卷等不同物品的堆放形式和存储要求,结合上述识别、定位、存取、监控等关键技术开发智能起重机的监控和管理系统MWS,包括接口子系统、货位库存管理子系统、物品识别子系统、调度与起重机运行子系统、空间定位子系统等,实现起重机智能化高效、安全的运行。
来源:
上一篇: 智能起重机的发展与优势
下一篇: 半导体防静电洁净室起重机